Диагностика запорно-регулирующей арматуры при помощи интеллектуальных позиционеров
К настоящему времени в промышленности наблюдается массовое и повсеместное внедрение высокотехнологичных решений, направленных на повышение безопасности эксплуатации промышленного и технологического оборудования, и особенно систем, представляющих повышенную опасность для экологии и жизнедеятельности человека. Это в первую очередь, газопроводы и нефтепроводы, химическое производство, атомная и тепловая энергетика. Немалую роль начинают играть в современной промышленности системы диагностики запорно-регулирующей арматуры (ЗРА), причём, заметная доля рынка встроенных систем диагностики арматуры принадлежит системам, основанным на использовании позиционеров. Цитируя интернет-источники, «Сегодня практически у каждого производителя позиционеров присутствует линейка цифровых продуктов, обладающих функциями диагностики».[1] Цифровые позиционеры для запорно-регулирующей арматуры это устройства, имеющие возможность отслеживать положение рабочего органа ЗРА и, как правило, обладающие возможностью следить за плавностью хода рабочего органа, правильностью его начального и конечного положений. Ряд позиционеров имеет возможность оценивать, говоря литературно, адекватность реакции ЗРА на управляющие сигналы. Целью этого является повышение быстродействия и отклика исполнительных механизмов путём включения обратной связи по положению выходного штока исполнительных механизмов ЗРА. Наиболее продвинутые модели производят запись большого количества данных о ходе циклов открытия-закрытия и регулирования ЗРА, сохраняют их в собственной памяти, общаются с управляющими системами посредством аналоговых и цифровых интерфейсов, имеют тесную интеграцию с блоками управления запорно-регулирующей арматуры. Некоторые простые модели позиционеров имеют цифровой индикатор или «светофор», позволяющий при отказе сразу увидеть аварийный сигнал, просто взглянув на устройство. Перечислим некоторых производителей и марки подобных устройств для запорно-регулирующей арматуры:
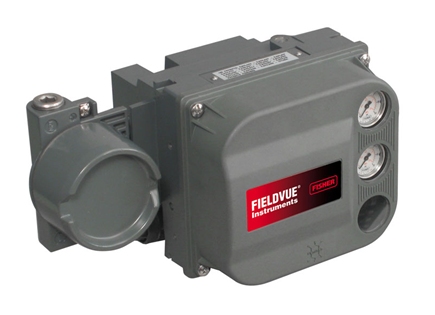
- Emerson (FIELDVUE)
- Flowserve (APEX)
- General Electric (Becker, Masoneilan)
- Metso Automation Inc. (Neles)
- Schubert Salzer (8049)
- SIEMENS (Sitrans)
- Young Tech Co. (YTC)
- Автоматика (ППМ)
В целом современные позиционеры решают такие задачи, как: увеличение быстроты и точности регулирования, экономия, в том числе на снижении числа обходов и осмотров при помощи полевого персонала, снижение аварийности и последствий аварийных ситуаций, снижение полной стоимости владения TCO, то есть в конечном итоге они повышают экономическую эффективность производства. Наличие в арматуре функций диагностики снижает нагрузку со стороны контролирующих органов. Общей и основной технической задачей, которая решается при помощи позиционеров, является определение качественных характеристик хода рабочего органа запорно-регулирующей арматуры и создание на основании этой информации заключения о работоспособности данной арматуры. Объектом данного заключения будет являться совокупность привода и самого устройства (крана, клапана, задвижки). Однако наряду с достоинствами данного подхода имеются проблемы выявления источника неисправности в комплексе привод+кран (клапан, задвижка). Это происходит по вполне очевидной причине, заключающейся в том, что невозможно определить источник механических проблем, в случае, когда два устройства объединены одним механическим приводом (штоком или валом). Опыт общения с представителями эксплуатирующих организаций свидетельствует, что замена всего комплекса как минимум экономически невыгодна даже с учётом того, что после ремонта или замены одного из элементов комплекса (например, только привода) как минимум половина данного агрегата может быть возвращена в строй. Существуют и другие причины, вот краткий перечень основных мнений и пожеланий эксплуатирующих организаций:
- Необходимо определить, что именно вышло из строя, кран или привод, чтобы знать, с каким набором запасных частей, материалами и инструментом необходимо прибыть к месту неисправности.
- Позиционер неспособен определить неисправность внутри пневмопривода, утечку газа или гидравлики (для гидропривода).
- Большая часть нашей запорной арматуры находится под землёй, поэтому эксплуатирующим организациям необходимо знать состояние крана, состояние привода менее актуально, поскольку привод легче диагностировать визуально (мнение представителей Газпрома). То же самое можно сказать по поводу клапанов, расположенных в опасных зонах на предприятиях Росатома.
- Касаясь состояния крана, необходимо определить в первую очередь не наличие проблем с перестановкой запорного органа в виде рывков итп, а возможность выполнения запорным краном функции перекрытия потока транспортируемой среды, в частности, целостность уплотнений.
Вместе с тем, конкуренция на рынке позиционеров породила варианты конструкций позиционеров, которые имеют сотни функций, большинство которых реально не являются значимыми и, скорее всего, никогда не будут вызываться во время их штатной работы. Для службы эксплуатации в общем случае достаточно было бы иметь на посту управления некий «светофор» или индикатор, отображающий показатель здоровья каждого элемента ЗРА. Подробная же графическая информация с указанием сотых долей процента по различным показателям скорее является пригодной только для изучения экспертами по запорной арматуре при исследовании динамики процессов.
В свете вышесказанного становится очевидно, что позиционер, или устройство, которое можно назвать диагностическим контроллером, должно обеспечивать:
- Простую базовую индикацию состояния
- Раздельную индикацию по приводу и по крану (клапану, задвижке)
- Индикацию утечек привода
- Индикацию утечек крана
- Детектирование неравномерности движения запорного органа
- Создание обратной связи для повышения точности регулирования с указанием рассогласования.
- Хранение при необходимости базы данных состояний арматуры
- Общение с АСУТП по проводам или по беспроводным технологиям
В рамках технологического проекта «Импакт Россия» была создана линейка продуктов, и решений, включающих в себя диагностические контроллеры для запорной арматуры, которые могут как сопровождать и дополнять своими функциями существующие интеллектуальные приводы с позиционерами, такие как FIELDVUE, так и работать самостоятельно, предоставляя собственный определённый функционал. Что такое Импакт? Импакт это диагностические приборы и технологии, позволяющие производить диагностику мостов, опор, трубопроводов, кранов, цилиндро-поршневых групп, клапанов, задвижек, скважин, буровых платформ, прочих машин и механизмов используя вибрацию, ультразвук, инфразвук, томографию, голографию, и прочие технологии. Например, диагностический контроллер Impact Built-In, предназначенный для установки на действующую арматуру или для комплектации вновь производимой арматуры, обладает следующими функциями:
1 Функция прослушивания шума перетока на закрытом кране/задвижке/клапане (базовая)
2 Функция вибрационного воздействия на ЗРА и прослушивания отклика (в закрытом и открытом положении)
3 Функция контроля состояния 2-х аналоговых датчиков и 5-ти дискретных входов (концевиков)
4 Запись показаний двух аналоговых входов, контроль наличия рывков и передача их на головную АСУТП для анализа
5 Функция обучения типичным шумовым картинам (SoundPrint) и выбор наиболее похожей на текущую шумовую обстановку
6 Функция вычисления спектральной плотности шума перетока и вычисление количества перетока в условных единицах
7 Анализ шумовой картины по методам 1 или 2 с использованием математической модели AudioDNA с вычислением качества крана в процентах.
8 Общение с головной АСУТП по интерфейсу Ethernet, протокол TCP/IP, возможно по Wireless LAN, GSM.
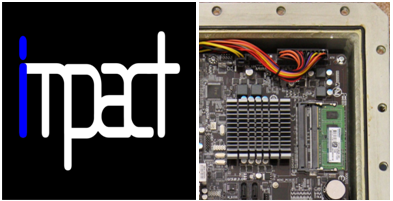
Диагностические контроллеры Импакт работают по классу методов ВД (вибродиагностика) в суперспектральном диапазоне частот. Кроме всего прочего, производство контроллеров Импакт расположено в России и согласуется с государственной программой импортозамещения.